Bay Industrial has a long history of providing high quality goods from the Far East to Western countries. More than 30 years ago, the company was producing sports balls such as basket and volley balls in Korea and had a separate commercial department that exported European-style furniture and decorative items for a US retail chain.
Bay Industrial has a long history of providing high quality goods from the Far East to Western countries. More than 30 years ago, the company was producing sports balls such as basket and volley balls in Korea and had a separate commercial department that exported European-style furniture and decorative items for a US retail chain. Seeing the opportunity to expand its expertise in precision cutting and assembly of fabric, Bay decided to enter the growing inflatable boat market in 1986.
In 1994, when Bay started to supply inflatable boats to the Brunswick Group, Bay moved the facility for ball production to China and focused the Korean factory on inflatable boat manufacturing. Since the beginning of the relationship, Bay has produced more than 190,000 boats for Brunswick under the Mercury and Quicksilver brands, plus a small series of Sea Ray and Bayliner branded tenders. Bay has also manufactured 40,000 boats under its own LodeStar brand (including a small series of branded tenders for Swedish builder Nimbus and US builder Ranger Tugs).
Other important activities include the production of tubes for UK luxury RIB tender builder Williams Performance Tenders, river rafts for the US market, and government patrol boats for African and Asian markets.
Today Bay is one of the world’s top manufacturers of inflatable boats, with three core competencies: highly mechanized assembly of PVC coated fabrics, hand assembly of Hypalon coated fabrics, and fiberglass resin transfer moulding (RTM) for small boat hulls. As a leader in the inflatable industry, Bay’s enthusiasm and passion for inflatable boats innovation know no measure.

Highly automated manufacturing with strict control standards optimum
temperature & humidity all the year around. This is especially important
for gluing processes (Hypalon boats). The building where gluing
processes takes place is controlled for both temperature and humidity -key
parameters that must stay within strict limits in order to guarantee
high quality seams. Many competitors do not control the manufacturing
environment which can lead to substandard product and early failures.
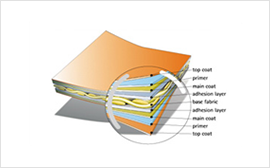
Duratex PVC fabric
Long-life: excellent resistance to cuts, abrasion and normal wear & tear
UV resistant: proven by actual weathering tests for years
Long-term relationship with a well established European supplier
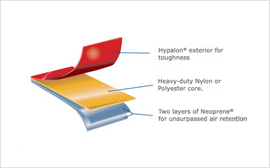
CSM fabric
Superior performance in most extreme conditions:
Resistance to abrasion, hydrocarbons, ultra-violet light and
fading CSM coating which goes over a super-tough synthetic fabric
and an inner layer of Neoprene
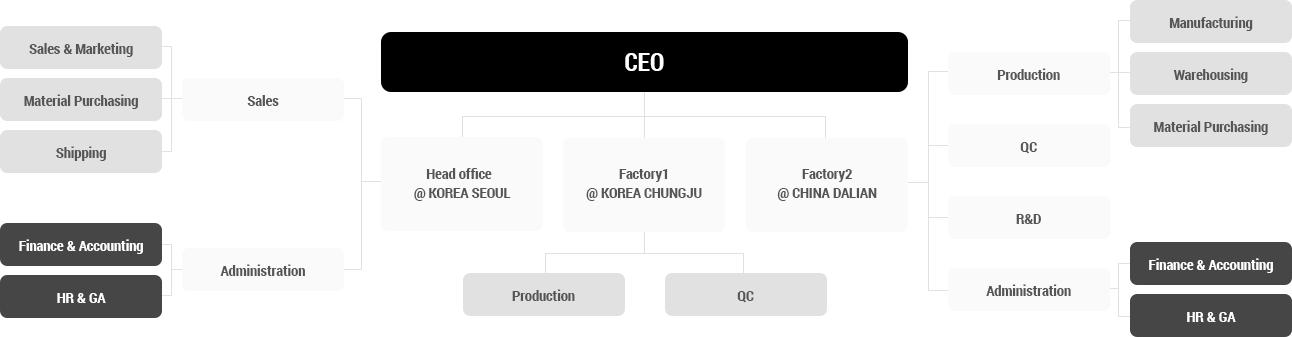
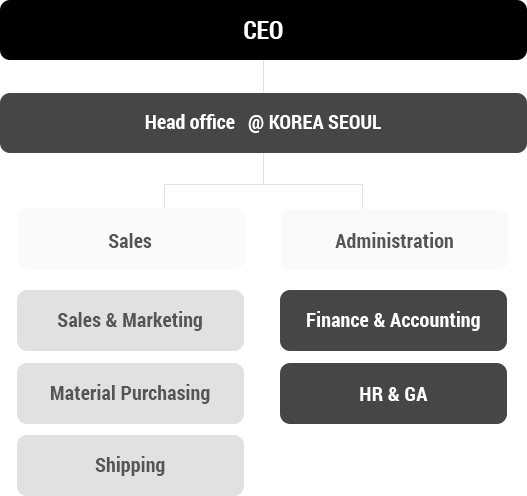

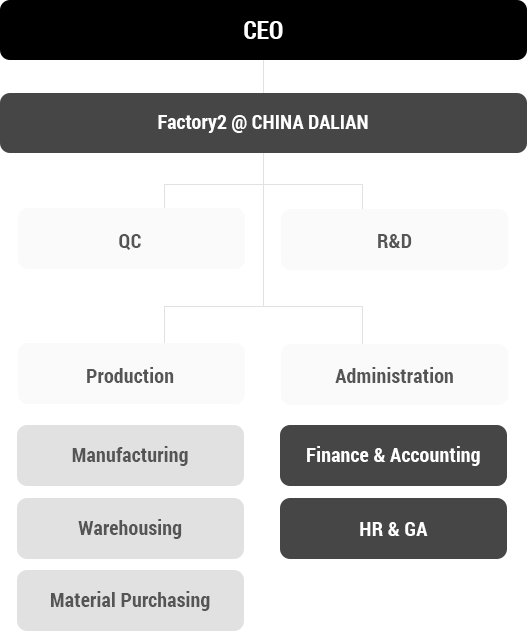
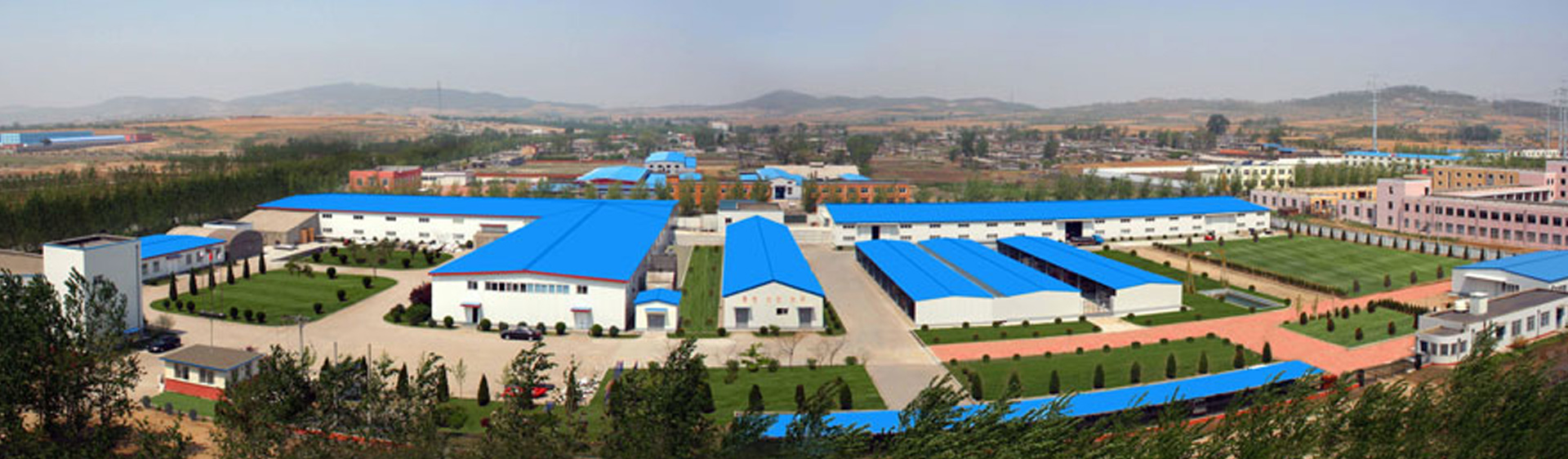
The factory is located in Dalian, in north-east of China. The complex in 35,000m2 complex consists
of six buildings covering an area of 13,000m2 (140,000ft2). Good ventilation systems, high ceilings and
containers of odour absorbing charcoal keep the facility worker-friendly.
Slide 1
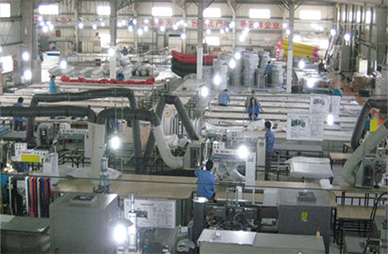
Overview of the cutting and thermal welding section of the
factory. In the background can be seen stacks of high pressure
air floors being tested for air leaks.
Slide 2
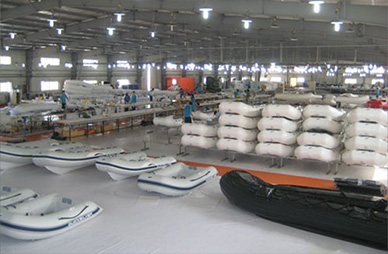
In order to maintain a clean environment, street shoes are not
permitted in the factory unless they are covered by disposable
protectors. Even then, they are only permitted on the orange
walkways, seen here in the Neoprene-Hypalon assembly hall.
Workers and visitors alike are required to be sock-footed on the
grey fabric working surfaces. Stacked boats are undergoing a 48
hour pressure check.
Slide 3
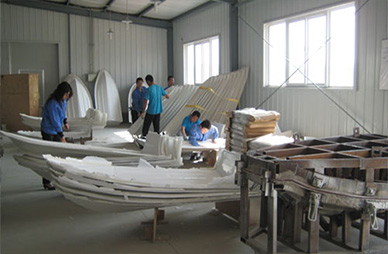
Small RIB hulls are built using RTM in specially reinforced moulds,
one of which can be seen on the right side of the photo. The hulls
stacked in the foreground are awaiting trimming after which
hardware will be installed prior to tube assembly.
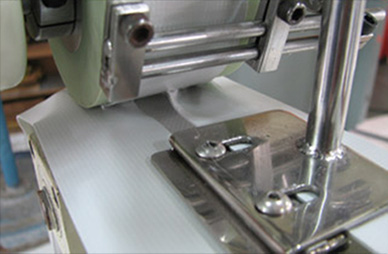
Hot air sealingline
seam. Thermal welded seams are even stronger than
the material itself. It provides a clean look for years,
free from contamination caused by glue spilled over
the seam line.

High Frequency weldingline
No chance to get excess glue marks which will turn
yellow with exposure to the sun.
Better adhesion and durability than gluing.
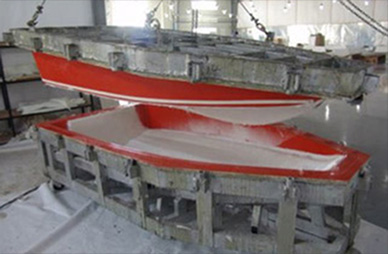
RTM(Resin Transfer Molding)line
hulls using RTM technology. Technical advice was
sought from both South Africa and Europe and hulls
were tested to destruction by Permay Prototypes and
Composites of Waukesha, Wisconsin in the US,
as part of Mercury’s quality assurance requirements.
Buoyancy
Inflatable boats tend to be more buoyant than traditional watercraft, mainly because of the inflatable collar
or tubes. The inflatable sections help spread the buoyancy out over the entire area of the boat, making it more
resistant to sinking. In addition, the collars or tubes on an inflatable boat are usually designed with separate chambers
so that if one chamber becomes deflated, the overall buoyancy will not be noticeably affected.
Stability
Unlike traditional V-hulled boats, an inflatable boat sits flat in the water and has a low centre of gravity, making
it virtually impossible to tip. It is better able to handle rough water, and people standing up in the boat
won’t cause the craft to capsize.
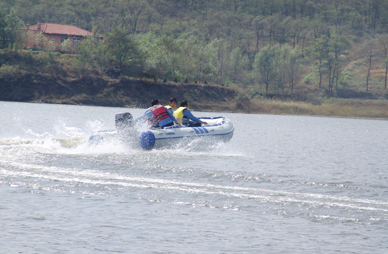
Testing is believingline
specifications, a prototype is required. Both it and at
least one actual production sample are verified for
performance by on-the-water testing before beginning
serial production.
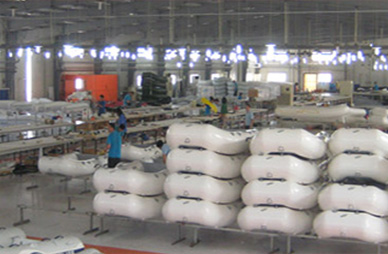
Air tightness testline
pressure at least 72 hours to ensure air tightness
of every chamber.
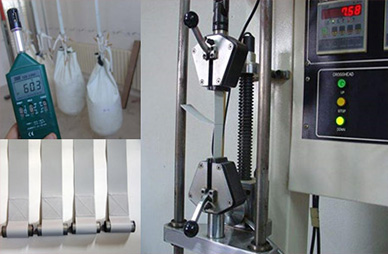
Test facilitiesline
equipped to do testing to ISO-6185 norms. Tests are
routinely performed include UV resistance testing,
seam strength testing and resistance to chemical
products such as fuel.
Drop test
Bay has an outdoor test tank where it performs drop tests as required
by the EU’s Recreational Craft Directive.
Self Inflation system – patented
Bay’s new self-inflation system is very simple, quick, convenient
and safe. It makes it possible to shorten the inflation time and
to save your efforts.
